Forklift Camera – Elevating Safety and Precision in Warehouse Operations
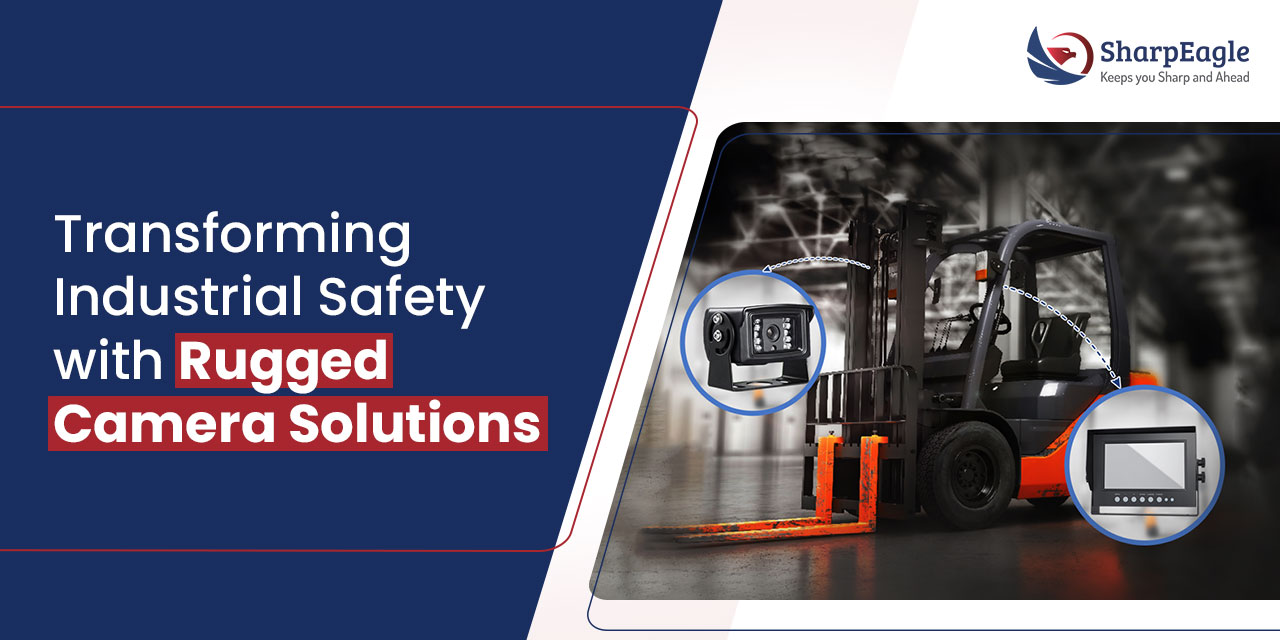
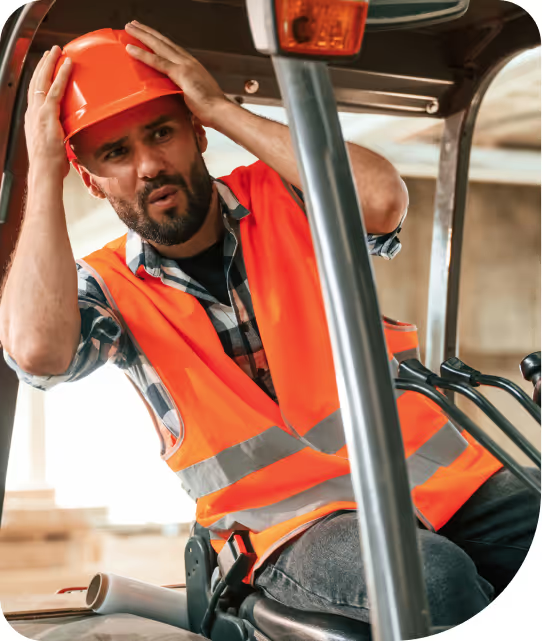
The Problem
The company’s operations faced several key issues:
- Limited Visibility: Operators had only partial visibility of the equipment’s surroundings, leading to increased accident risks and inefficiencies.
- Manual Monitoring: Traditional methods did not provide the real-time, comprehensive view required for safe operations.
- Safety Hazards: Without clear views of blind spots, the risk of accidents was heightened, compromising both personnel and equipment safety.
- Productivity Impact: Poor visibility slowed down operations and led to inefficiencies in maintenance and day-to-day tasks
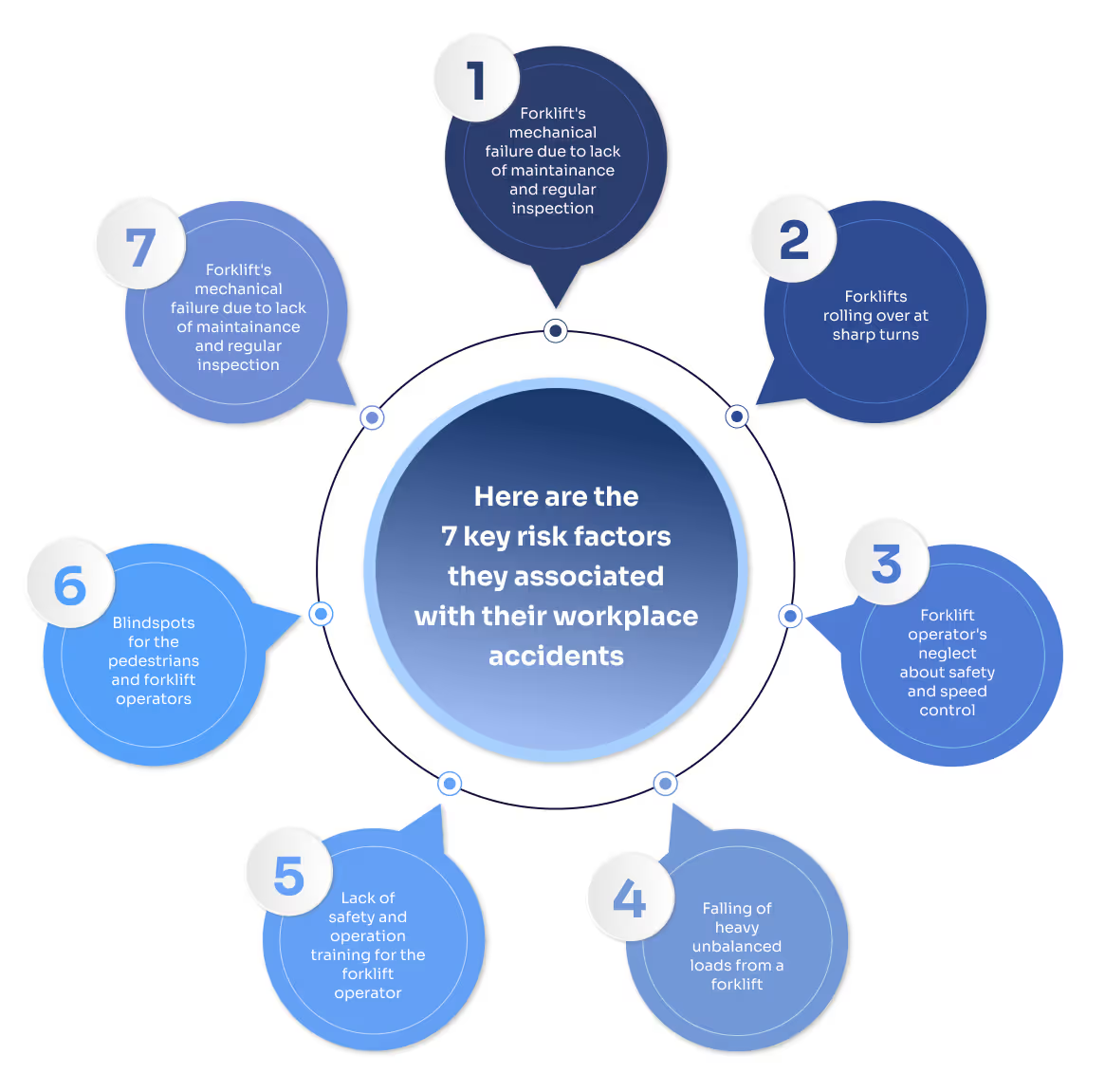
Specific statistics prior to the installation included:
- Increase in Accident Reports: A 15% rise in reported near-misses due to visibility issues.
- Slow Maintenance Response: Maintenance delays averaged 3 hours per incident due to the inability to quickly diagnose equipment issues.
The Solution
SharpEagle’s rugged camera system provided a comprehensive solution to these challenges, significantly enhancing operator visibility and safety. The system consisted of:
- Installation of Four HD Cameras: Four high-definition rugged cameras were strategically placed around the Kalmar equipment, offering full 360-degree coverage.
- Monitor and MDVR Installation: A 7-inch monitor installed in the operator's cabin displayed real-time footage, while an MDVR recorded all operations, storing up to 500 hours of footage for future review.
- Durability and Low Maintenance: The rugged cameras were specifically designed to operate in harsh conditions, withstanding temperatures ranging from -20°C to 60°C and reducing the need for regular maintenance by 30%.
- Low-Cost, High-Impact: The total installation cost was 20% lower than alternative CCTV systems, and the system required 50% less time for installation compared to traditional setups.
.avif)
Recommended Product Investments
Training Modules: To optimize operator’s understanding of forklift operations, along with use and application of other safety measures installed on forklifts
Safety Videos: To ensure crew and operator’s daily safety measures and safety protocols in case of an accident or an emergency.
Monthly Safety Checks: To detect any potential malfunction in the machinery, avoiding accidents beforehand.
The Results
Following the installation of SharpEagle’s rugged camera system, the company experienced measurable improvements:
- Enhanced Operator Safety: The real-time visibility provided by the cameras reduced the number of near-miss incidents by 25%, significantly improving operational safety.
- Improved Efficiency: Operators were able to complete inspections 40% faster, reducing downtime and improving overall productivity. The ability to monitor blind spots in real-time cut the average incident resolution time from 3 hours to 1 hour.
- Detailed Documentation: The MDVR allowed the company to maintain a visual log of all operations, increasing accuracy in reporting safety compliance and equipment conditions. Over 100 hours of footage were reviewed for maintenance purposes within the first month.
- Cost Savings: By avoiding the need for more complex CCTV installations, the company saved £10,000 in installation costs, while also cutting down on future operational costs related to safety incidents and maintenance delays.
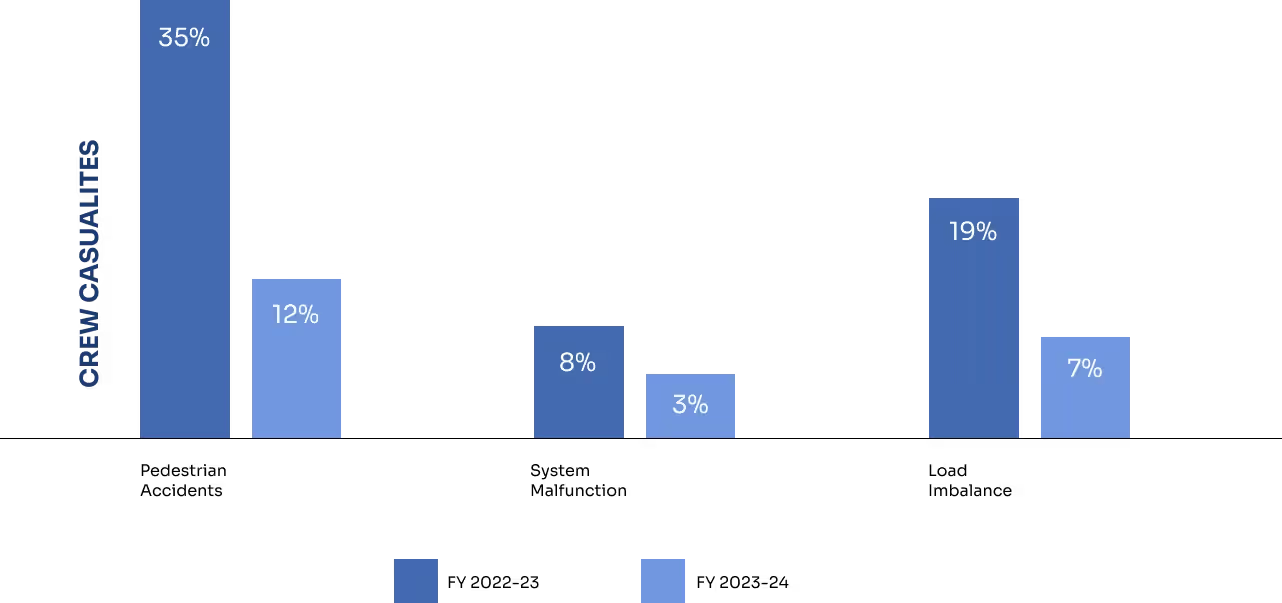
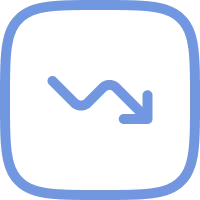
Decline in Accidents by
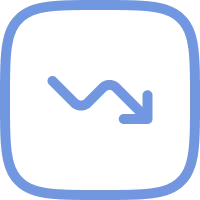
Decline in Accidents by
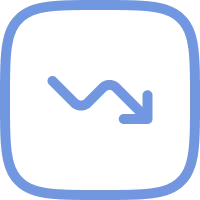
Decline in Accidents by
Conclusion
The implementation of SharpEagle’s rugged camera system provided the company with a significant boost in both safety and efficiency. The portable, high-definition camera solution reduced risks associated with poor visibility, allowed for faster incident resolution, and improved overall operational efficiency. By integrating this cost-effective, durable solution, the company avoided the complexities and high costs of traditional CCTV installations, ultimately leading to a safer, more streamlined operation.
For more information on how SharpEagle’s wireless Forkview Camera System can enhance your warehouse operations, visit our website or contact us directly.
To recreate such safety trends for your workplace
Contact Us Today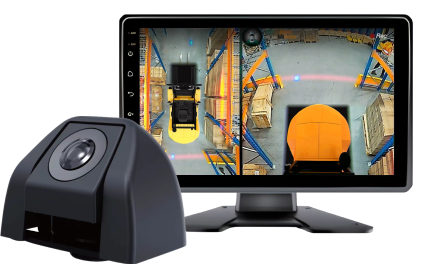
For more information on how SharpEagle’s Forklift Camera System can enhance your warehouse operations, visit our website or contact us directly.
To recreate such safety trends for your workplace
Contact Us Today*Note: The statistics presented in the case study are accurate, verified, but rounded off. The name of the company has been changed for privacy reasons. Any resemblance of the used fictitious company name with an established corporation is not intentional and merely a coincidence.